CONTINUOUS IMPROVEMENT MODEL CASE STUDY Innovative change management them with time to discuss upcoming change coaching and tracked supplier progress. To “The 100-day project process leads to improved management work and any challenges and/or leverage the learning as much as possible, Dell with Dell’s supplier achievements in implementation. promoted industry best practice sharing and resulted in several safety With each step in the process, the team actively cross-learning among suppliers in the area. The communicated information about the TenSquared innovative TenSquared framework for challenges successes. Managers As part of our ESG goals, we are committed to is more sustainable than a traditional approach ongoing engagement with the people who make program with other departments and senior and has increased the mutual trust between Dell were very responsive our products. This commitment requires ongoing management to obtain maximum support and and our suppliers. and workers showed support and partnership with our suppliers. cooperation. The 100 days of focus paid off in improved occupational health standards (OHS), As a result of the efforts and OHS innovation, great passion for jointly In FY22, we worked with Social Accountability as well as new processes and procedures: the supplier increased the rate of workers’ identified improvement International (SAI) to leverage a unique change compliance with safety behaviors from 79.0% management program. Using the TenSquared • “Blue Vest” observer roles were implemented. to 95.2%, which they maintained into FY23. The goals. Thanks to mutual approach, a peer-elected team of supplier These workers, wearing blue vests, are program has also encouraged workers to engage employees and managers collaboratively work to responsible for reminding and assisting in fixing OHS issues and has inspired more respect, partnership identify root causes of workplace challenges and colleagues who are not fully meeting OHS communication, respect and recognition. and collaboration then identify ways to resolve them. The timeline personal behavior standards. New hires and is 100 days; the goal is to find innovative solutions recent graduates have especially benefited from this supplier quickly to drive continuous improvement. the reminders these role models provide. identified and We engaged one of our suppliers in China to • Inspired by the program’s momentum, top addressed critical partner with us in using the TenSquared approach management also invested in developing safety issues. We to identify and address their environmental, efficient monitoring equipment. This technology health and safety (EHS) management concerns. helps take the program results to the next level appreciate Dell’s The supplier’s peer-elected team found several by enabling improved safety practices for shifts leadership in making challenges to address, including workers not around the clock. wearing personal protective equipment (PPE) • Launch and mid-point workshops for other this opportunity and not following other safe working procedures. factories in the area included best practice available in their During the 100 days, our supplier’s team applied sharing. After observing the improvements supply chain.” the TenSquared tools and methods they learned this supplier experienced, other factories in the to their internal training and evaluation processes. area have been inspired to implement similar JANE LIU The team also followed a work plan, offered each approaches. SOCIAL ACCOUNTABILITY other timely feedback and clearly defined the INTERNATIONAL division of responsibilities. The weekly coaching Throughout the process, our social and meeting was especially helpful as it provided environmental responsibility specialists offered INTRO OUR PLAN GOALS DASHBOARD ADVANCING SUSTAINABILITY CULTIVATING INCLUSION TRANSFORMING LIVES ETHICS & PRIVACY SUPPLY CHAIN BY THE NUMBERS APPENDIX DELL TECHNOLOGIES 111 FY22 ESG REPORT
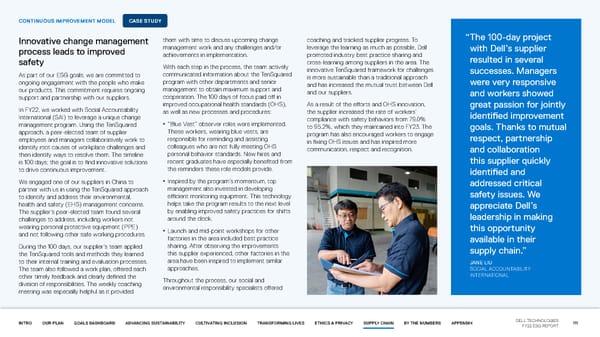